Case Study: Revolutionizing Fragrance Production with Stainless Steel IBCs in the Northeast
Introduction
Discover how a New Jersey-based fragrance company transformed its manufacturing process with stainless steel Intermediate Bulk Containers (IBCs). This case study explores the company’s challenges, solutions provided by stainless steel IBCs, and the remarkable outcomes achieved in the fragrance industry.
Background Company Overview
Founded over three decades ago, this New Jersey-based fragrance company specializes in creating premium scents for perfumes, cosmetics, and household products. With a strong commitment to quality and innovation, the company continually seeks advancements in its manufacturing processes.
Initial Challenges:
Solution: Stainless Steel IBCs
To overcome these challenges, the company transitioned to stainless steel IBCs known for their durability and efficiency.
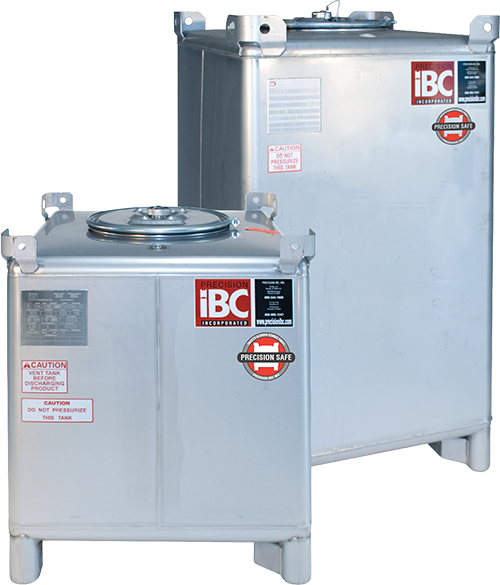
Key Features of Stainless Steel IBCs:
Implementation Transition Process:
The company partnered with a leading stainless steel IBC rental provider to facilitate a seamless transition
Outcomes:
Conclusion
The adoption of stainless-steel IBCs marked a significant milestone for this New Jersey fragrance company, setting new standards in operational efficiency and sustainability. This case study demonstrates the transformative impact of innovative solutions on manufacturing processes, inspiring others in the fragrance industry to enhance operations and environmental practices.